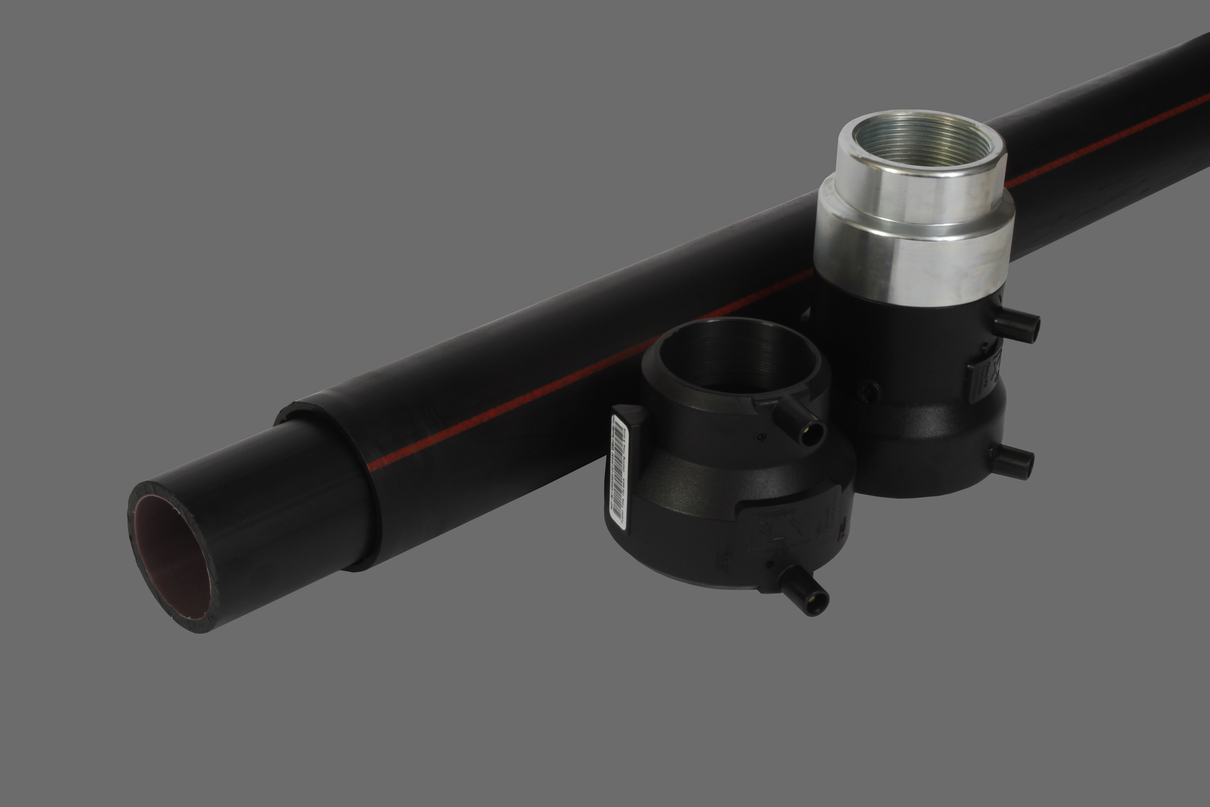
Product:
PLX
Solution:
Safe fuel conveyance
Project:
Lowestoft Haven Marina
Installer:
Allerton Marine Services
The Challenge
Lowestoft Haven Marina is a marina situated on the coast of East Anglia. In operation all year round, it is essential that the berthed boats have a reliable pipework system to feed the fuel dispensing units on the pontoon. Allerton Marine Services needed to source a new pipework system that was safe and longer lasting, as well as ensuring that no harmful emissions can escape into the environment.
The Solution
After careful research, the contractor decided to opt for a plastic pipework solution. Fuel permeation resistant, durable, lightweight and flexible, plastic pipework systems require significantly less energy to manufacture, transport and install than traditional pipework materials.
Richard Allerton, Director at Allerton Marine Services, said: “As Aliaxis are specialists in plastic pipework systems, we approached the company to see if they could offer us a solution for fuel transfer. With a 30-year design life, we were recommended the Close-Fit system from the PLX range, which provides a secure environment for the conveyance of marine fuels. It is corrosion and permeation resistant, as well as maintenance free, and as the pipe is secondary contained, it provides security against accidental fuel leaks and losses. As this ticked all of the boxes, we knew that it was the ideal solution for the marina.
“Prior to installation, we were invited to the factory to complete installation training, where our installers spent the day with the Aliaxis team and were shown how to correctly install the pipework system and fittings using the appropriate tools.”
The PLX Close-Fit system installed at the marina
The PLX Close-Fit Pipe System in size 50#63mm was installed at Lowestoft Haven Marina, which runs from the 10,000ltr tank on the marina down to the fuel dispensing unit on the floating pontoon. The pipe was run through 14m of 3” NB galvanised pipe across the boat lifting dock for extra protection and then dropped down onto the floating pontoon and placed into the service duct for a 50m run. The pipe then terminates at the containment tray underneath the fuel dispenser. Thanks to the installation of secondary containment fittings, this allows interstitial monitoring and leak detection of the complete system.
Richard continued: “There are lots of key features and benefits of the PLX system. We are really pleased with the secondary containment pipework and the fact it enables us to monitor the system and detect a leak is extremely beneficial. The transition from steel to plastic was certainly the right choice and I am sure this will also be proven in the years to come. The Aliaxis team were a great support throughout the project and we can’t fault their services.”
The smooth bore of the PLX plastic pipe ensures less friction build-up and guarantees a consistent flow rate is maintained throughout the life of the system. With optimum flow levels maintained, minimal maintenance and repair work is required to ensure the system operates efficiently.
For more information on our PLX fuel transfer system click here.